The wood peeling machine can effectively remove the bark of the wood, and will not cause too much damage to the wood itself. This machine has strong applicability to wood. It can peel wood of different tree species, diameters, lengths, and shapes.
Using the wood peeling machine can greatly save the labor force and reduce the cost of raw material processing. So what factors will affect the peeling effect and how to make the machine run more efficiently? Here is the answer.
The six factors that affecting the peeling efficiency

- Machine power: The power of the motor needs to be able to drive the normal operation of the equipment without jams or shutdowns.
- The humidity of wood: Generally speaking, drying wood for a period of time after cutting can significantly improve the effect of peeling. In addition, the season also has a certain influence on the peeling rate of wood. Compared with winter, the wood will be drier in summer, and the peeling effect will be more significant.
- Wood bending degree: For the trough-type peeling machine, if the wood bending degree is too large, the bark of the bent part cannot be separated because it cannot contact the peeling teeth. Generally, the bending rate is less than 8%. For the vertical peeling machine, the degree of curvature of the wood doesn’t matter.
- Wood material: Different wood materials will also have a certain impact on the peeling effect. For example, the peeling effect of willow and fir is relatively better.
- The smoothness of the wood: If there are wood bumps or branches on the surface of the wood, it will also reduce the peeling effect of the wood.
- Degree of equipment automation: The wood peeling machine can be equipped with an automatic feeding and discharging system, and a conveyor belt can also be equipped under the machine to transfer the bark stacked underneath in time.
Tips of wood peeling machines
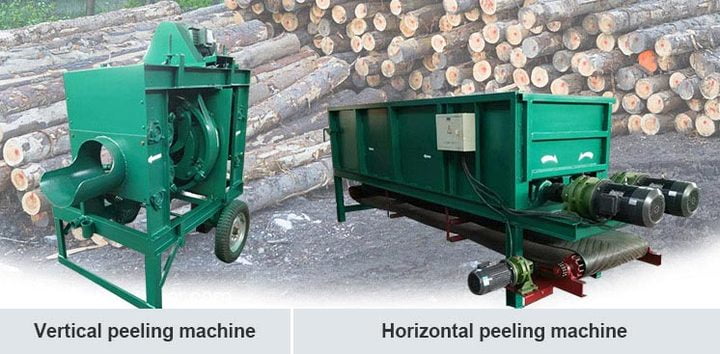
- To give full play to the performance of this machine, there should be no less than 2 operators.
- There should be no iron, stone, and other sundries in the material with the guillotine.
- When working, properly adjust the amount of material fed, too much will easily cause overload and stop, and too little will affect the cutting efficiency.
- If there is a blockage during work, it is not allowed to forcibly feed it by hand or iron rods, and it should be shut down immediately to clear it.
- During work, if an abnormality is found or an abnormal sound is heard, the machine should be shut down for inspection immediately, the power supply must be cut off before the inspection, and it is forbidden to troubleshoot while the machine is running.
- Each movable part is filled with butter once a day, and the main bearing needs to be filled with lithium-based grease once when it is used for 300 hours.
- When you stop working, let the machine run idling for two minutes, blow off the dust and weeds in the machine, and then shut it down.