The feed pellet machine is a kind of equipment mainly used to make animal feed, generally using biomass such as soybeans, forage, straw, rice husk, and corn as raw materials. After the material is crushed and stirred, the pellet machine will extrude them into particles with uniform size and neat shape. The smooth-grained feed processed by this machine has a smooth surface, moderate hardness, low-temperature rise during processing and can better maintain various nutrients inside the raw material. This machine is mainly suitable for the processing of fish, duck, chicken, shrimp, rabbit, pig, cattle, sheep feed pellets. The diameter of the particle size can be customized according to the needs of different growth periods of the farmed animals. This machine has a simple structure, low noise, wide applicability, it’s the ideal equipment for the livestock feed pellet.
Structure of the animal feed pellet mill
This machine is mainly composed of the power unit, inlet and outlet, press roller, and pressing plate. Among them, the power unit can be driven by an all-copper motor or a diesel engine. It is equipped with a geared motor, which can obtain greater torque while reducing the speed. The size of the discharge port can be customized according to customer needs.
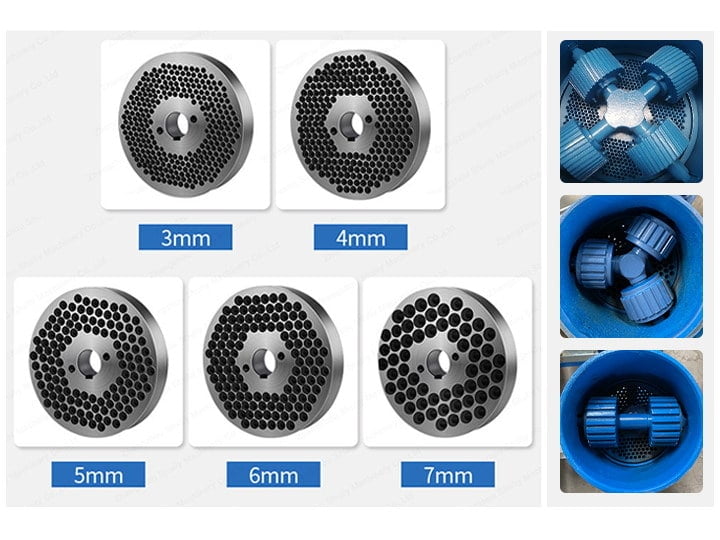
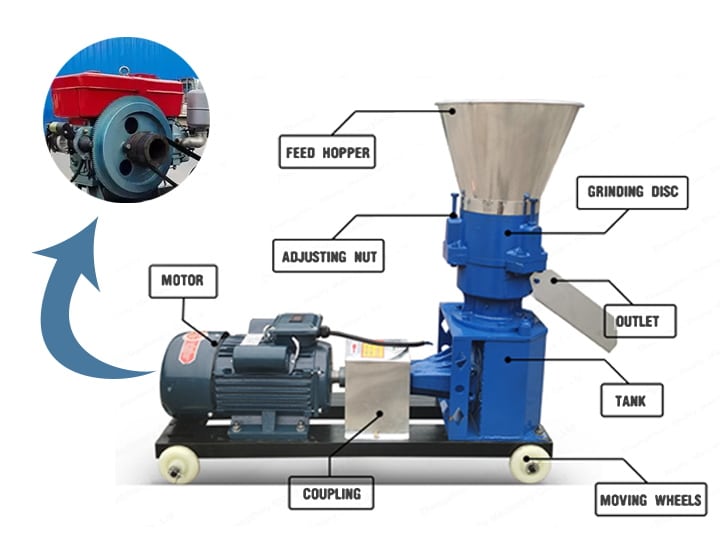
There are usually two-roller, three-roller, and four-roller models of press rollers. The more the number of press rollers, the greater the output. The aperture range of the pressing plate is usually between 3mm-8mm. The smaller the processing diameter of feed pellets, the smaller the output.
The principle of the pelleting machine
The main components of the flat die pellet machine are a flat round steel die and a set of freely rotatable grooved rollers. The raw material falls into the gap between the rollers under the action of its own gravity and the rotating distributor, and is crushed into the die hole by the rotating roller. Then the long cylindrical material is extruded from below the die hole and cut into pellets by the cutter. In the granulation process, the high temperature generated by the friction will kill the bacteria in the raw material, and will not affect the quality of the granulation.
The advantages of the Livestock Feed Pellet
- Animal feed pellets are comprehensive in nutrition, animals are not easy to picky eaters, and the separation of nutrients is reduced.
- Pelletized feed is conducive to full digestion, absorption and utilization of livestock and poultry, and improves the digestibility of feed.
- After high temperature sterilization, reduce the possibility of feed mildew and insects, and improve the palatability of feed.
- Strong stability, not easy to collapse in the water, not easy to pollute the water body.
- Small size, not easy to disperse, not easy to be damp, easy to store and transport in bulk.
What are the raw materials of animal feed pellets?
The raw materials of animal feed pellets mainly include corn, soybeans, bran, rice bran, broken rice, sorghum, fish meal, soybean meal, cotton meal, rapeseed meal, grass, etc.
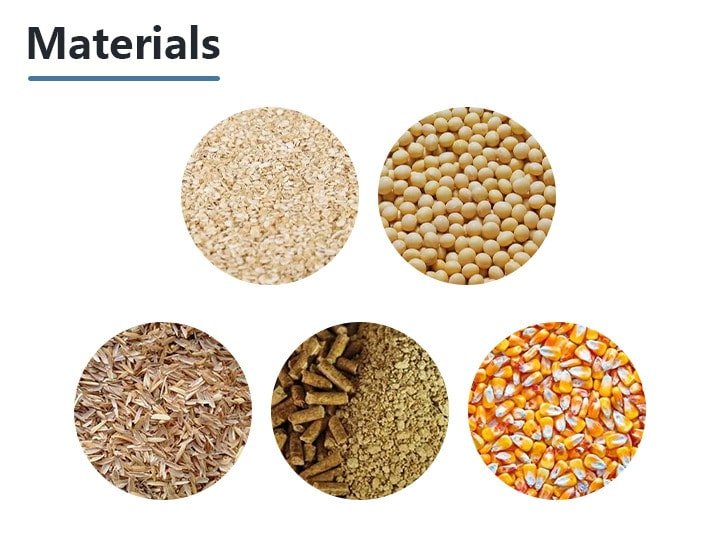
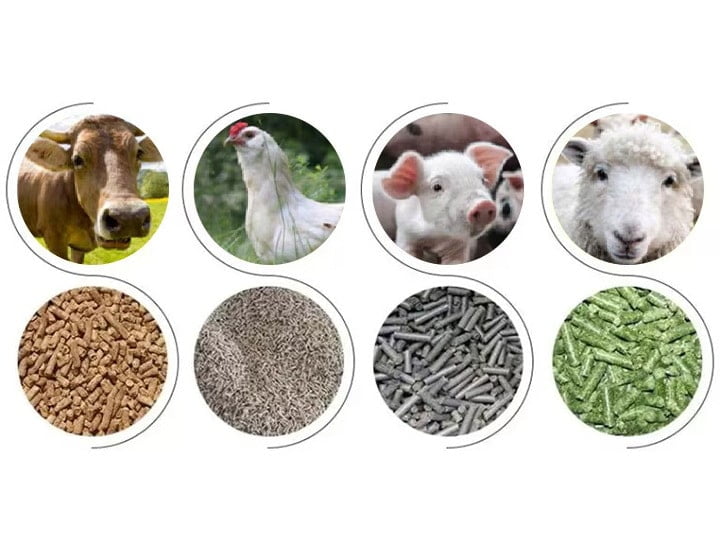
For different livestock at different growth periods, the choice of feed is also crucial. A reasonable feed ratio not only has good palatability and nutritional value but also can improve the digestibility and utilization of feed.
Parameter of the Pelleting Machine
Model | Power | Output | Dimension |
WD-125 | Single-phase, 4kw | 80-100kg/h | 850*350*520mm |
WD-150 | Single-phase, 4kw | 100-150kg/h | 850*350*570mm |
WD-210 | Three-phase, 7.5kw | 300-450kg/h | 990*430*710mm |
WD-260 | Three-phase, 11/15kw | 600-800kg/h | 1300*450*1100mm |
WD-300 | Three-phase, 22kw | 1000-1200kg/h | 1360*570*1150mm |
WD-400 | Three-phase, 30kw | 1500-1800kg/h | 1550*620*1250mm |
Tips of the animal pellet machine
- The gearbox can be turned on after adding hypoid gear oil.
- Install the pellet machine steadily, turn it in the direction indicated by the arrow, check whether the screws in each position are loose, loosen the adjustment screw on the roller shaft seat, so that the feed machine is in a no-load state, and it can be put into use after it starts and runs normally.
- Before the first use of the new machine, take 10 kg of sawdust (or grass powder) and 1 kg of surface sand mixed with engine oil as the new machine’s grinding material and mix well, and turn the gap adjustment screw to make the two rollers have the same speed. Gradually add abrasives, while continuing to turn the pressure wheel adjustment screw until the pellets are slowly discharged. The extruded pellets are repeatedly rolled to make the die hole smooth and smooth, and then slowly add the mixed feed to be processed for processing, such as feeling die The hole resistance is large, the output is low or the material is not discharged. The template can be repeatedly ground according to the above method to make the mold hole smooth and smooth before processing.
- When the feed is processed, if there is more refined fiber, about 5% of water should be added. If there are more concentrated materials in the mixed feed, the amount of water added can be reduced as appropriate. When the processing is completed, the remaining material is about 5 kg, add a little before The grinding material is beneficial to the next startup and avoids the feed f in the hole after the shutdown, otherwise the remaining material in the template hole is removed after the machine is filled.
- After processing, loosen the adjustment screw to make the rollers in a free state. After the machine stops, remove the remaining material deposits in the upper and lower bins, especially the remaining material under the swing plate to avoid damage to the bearing.
Matters needing attention
- When using, pay attention to the fact that there are no foreign objects such as stones and iron in the raw materials. After more than ten shifts of work, the pressure roller must be disassembled, and high temperature grease should be added to the bearing to make the roller work well and prolong the service life of the bearing.
- During granulation, it is strictly forbidden that the pressure roller and the template contact idling, and the continuous feeding can not be interrupted. At the same time, lock the pressure roller shaft nut to avoid loosening and damaging the spindle keyway.
- If the pellets are broken or not compacted, the crude fiber feed formula should be reduced to less than 50%.
- When there is no granulation or discharging during granulation, the template should be removed, and after opening it hole by hole, add some fiber feed to restart the machine for granulation.
- Frequently check the tightness of the screws in each part of the machine, replace the oil seal in time if the gearbox has oil leakage, and check whether the bearings in the machine head are short of oil.
- When the pellet machine is working, do not reach into the feeding port with your hands. If necessary, use wooden sticks to help feed the pellets.
- Before starting the machine, add less material before starting the machine. When shutting down, leave a small amount of feed in the machine to prevent the press roller of the machine from contacting the template from idling.
- If the machine is stuck when it is working, it should stop immediately, press the pressure roller until the bolt is loosened, and then restart the machine.
- Each time the work is completed, the adjusting pressure roller bolts must be loosened.
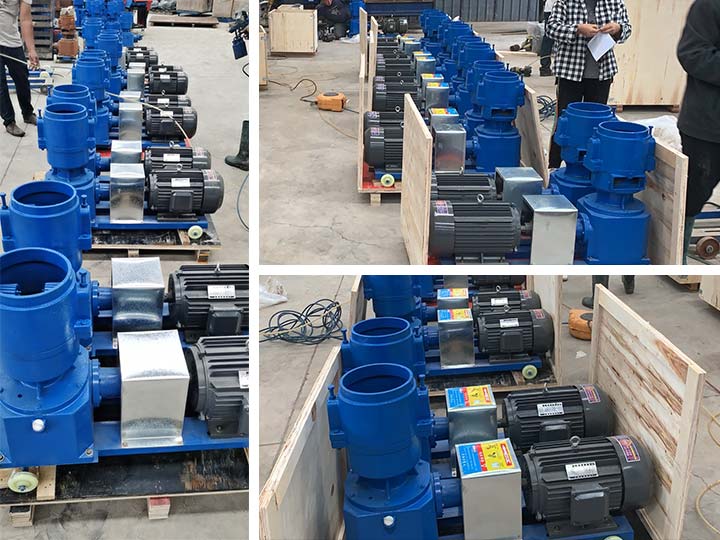
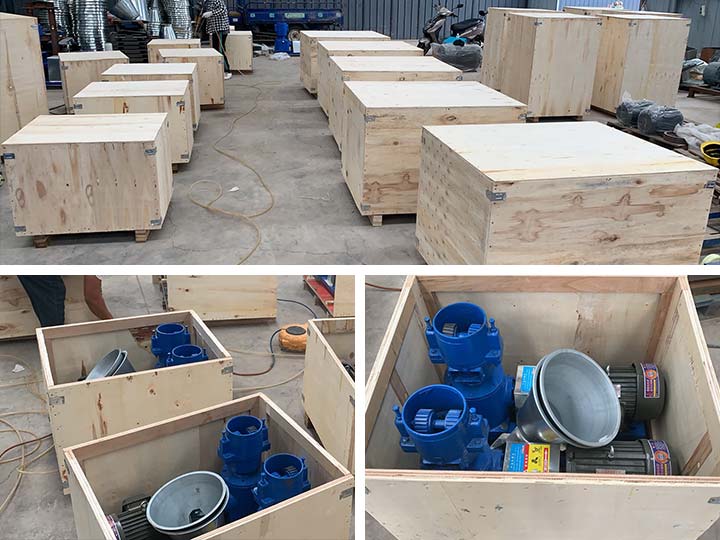