목재 팔레트 블록 제조 장비는 목재 칩, 부스러기, 짚 등의 폐기물을 원료로 건조, 접착제 혼합 및 가열 및 가압을 위한 열 프레스를 통해 팔레트 풋 블록을 생산합니다. 대부분의 원자재는 목재 가공 중에 발생하는 폐기물 스크랩이므로 최종 팔레트 풋 블록도 환경 보호 제품입니다. 또한, 고온, 고압을 거쳐 형성된 목재 팔레트 블록은 일반 단단한 목재 재료와 비슷한 경도를 갖습니다. 외관이 매끄럽고 평평하며 나무 팔레트에 발판과 다리를 만드는 데 이상적인 재료입니다. 우리의 압축 목판 제조 기계는 고객의 요구에 따라 크기를 맞춤 설정할 수 있으며 목판의 압력과 밀도도 조정할 수 있습니다. 고객의 요구를 완벽하게 충족시키는 고품질 기계입니다.
압축 목재 블록 제조기의 구조
우리의 압축 목재 블록 제조 기계는 주로 접착제 혼합 장치, 제어 시스템, 유압 시스템 및 가열 시스템으로 구성됩니다. 건조된 나무 조각이나 부스러기를 접착제 믹서에 넣은 다음 요소-포름알데히드 수지를 첨가하여 혼합합니다. 재료는 공급 포트에서 들어가고 나사의 작용에 따라 아래의 유압 탱크로 들어갑니다. 유압 시스템은 혼합 재료를 배출 장치 안팎으로 짜내고 배출 장치에는 가열 시스템이 포함되어 있습니다. 재료의 리그닌은 고온, 고압의 조건에서 용해되어 재료가 서로 단단히 결합되고 최종적으로 출구에서 나무 스트립이 형성됩니다.
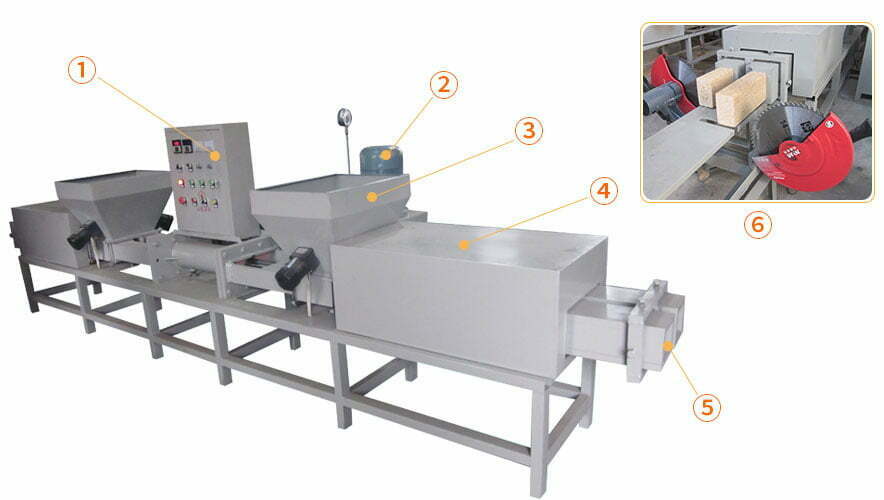
- 제어판은 기계의 유압 드라이브와 온도를 제어할 수 있습니다.
- 이 부분은 유압 시스템이고, 작고 둥근 부분은 압력 게이지입니다.
- 하역을 돕기 위해 내부에 나선형 교반 장치가 있는 하역 장치입니다.
- 가열판은 이 부분 내부에 있으며 온도는 약 200도입니다.
- 최종 제품이 이곳으로 배출되며 주변 나사로 압력을 조절할 수 있습니다.
- 고객의 요구에 따라 목재 스트립에 특수 블록 절단기를 장착할 수 있습니다.
목재 팔레트 블록 제조기의 장점
- 원재료는 목재 가공 과정에서 발생하는 폐목재 부스러기를 사용하고, 생산된 제품은 검사 및 훈증을 거치지 않아 친환경적인 제품입니다.
- 제작된 목판의 표면은 매끄럽고 평평하며 방수성이 있고 쉽게 깨지지 않습니다.
- 금형은 고객의 요구 사항에 따라 맞춤 설정할 수 있습니다. 목판의 밀도는 최대 700kg/m까지 조절 가능합니다.3, 강하고 못을 박을 수 없습니다.
- 장비 구조는 지속 가능한 개발 개념에 맞춰 간단하고 작동하기 쉬우며 시장 전망이 넓습니다.
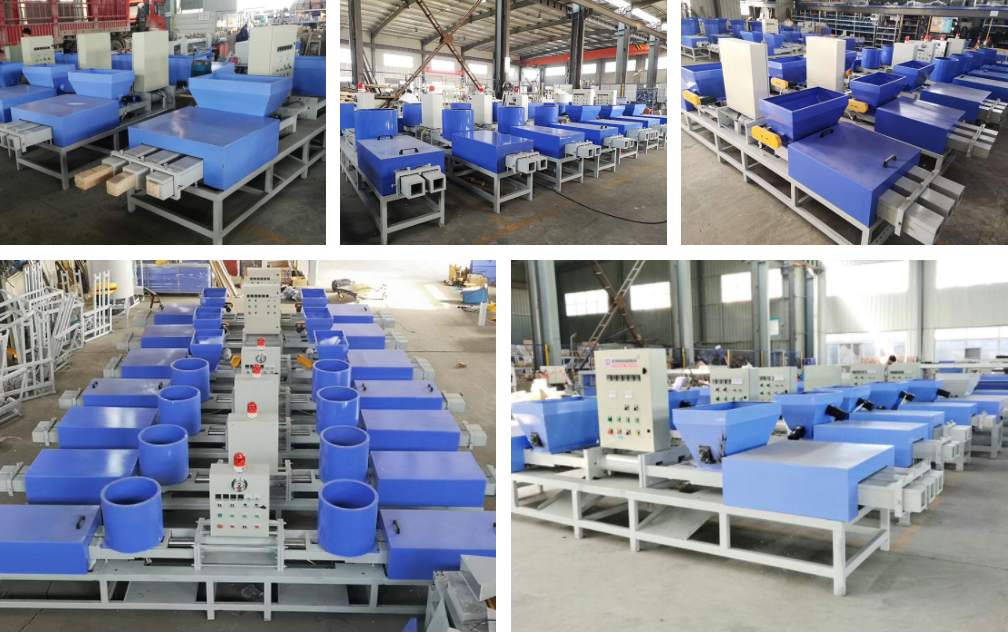
목재 팔레트 블록의 응용
목재 팔레트 블록은 주로 운송 산업에서 사용되며 우수한 보호 기능을 수행할 수 있습니다. 물류, 기계 및 전자, 세라믹 건축 자재, 하드웨어 및 전기 제품, 정밀 기기, 광업, 철강, 운송 및 기타 산업 분야의 제품 운송의 외부 포장 및 팔레트 처리에 널리 사용됩니다.
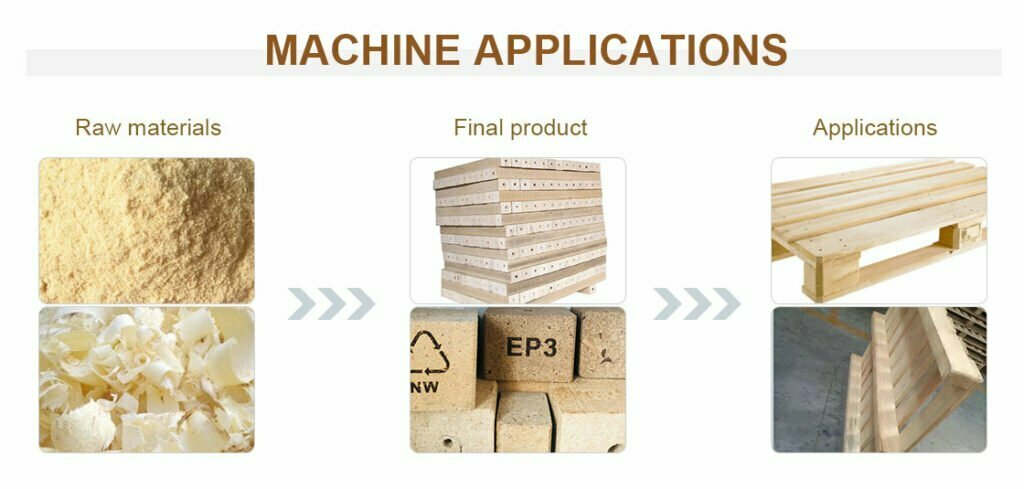
목재 블록 제조기의 매개변수
기계에는 유압 시스템과 두 대의 절단기가 장착됩니다.
모델 | 크기(mm) | 전력(kw) | 용량(m3/24시간) | 밀도(kg/m3) | 치수(mm) | 무게(kg) |
WD-75 | 75*75 | 15 | 3.5 | 550-600 | 4500*750*1200 | 1300 |
WD-90 | 90*90 | 15 | 4 | 550-600 | 4800*900*1200 | 1500 |
WD-100 | 100*100 | 16 | 6 | 550-600 | 5000*1000*1200 | 1800 |
WD-120 | 120*120 | 18 | 9 | 550-600 | 5500*1200*1200 | 2000 |