요즘 세계는 에너지 절약과 배출 감소를 주창하고 있습니다. 공장에서도 생산원가를 절감할 수 있는 방법을 모색하고 있으며, 다년간 건조설비의 생산 및 제조에 종사해 온 제조사로서 보다 에너지 절약형, 친환경적인 건조설비를 생산하기 위해 지속적인 노력을 기울이고 있습니다. 장비 사용 비용이 절감되고 사용자는 이점을 누릴 수 있습니다. 톱밥 건조기의 연료비를 줄이는 방법을 여러분과 공유하고 싶습니다.
톱밥 건조기의 연료 손실에 영향을 미치는 요인
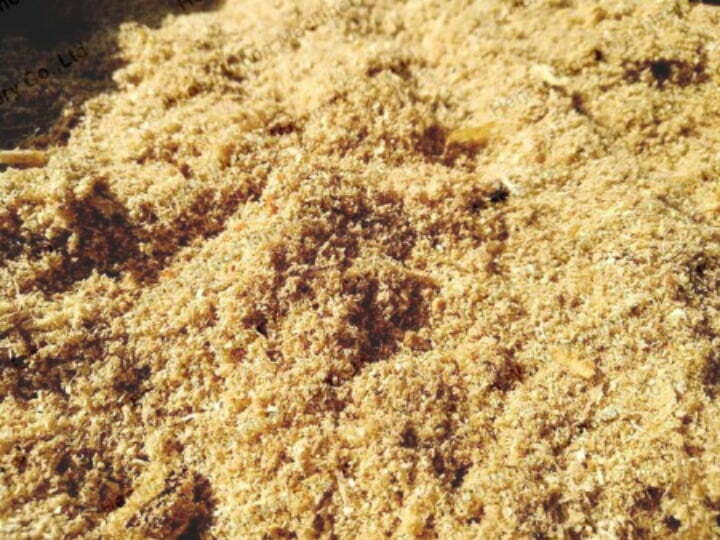
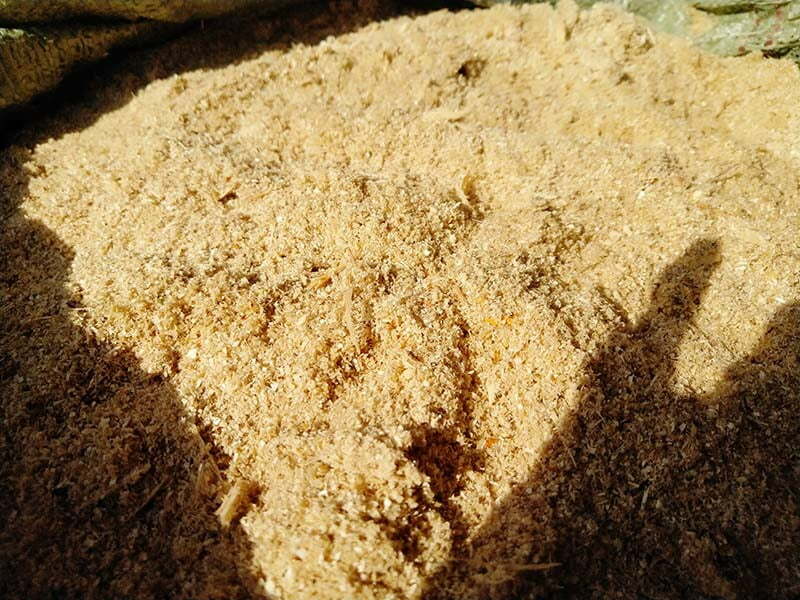
일반적으로 톱밥 건조기의 열원은 석탄입니다. 석탄 사용 비용을 줄이려면 석탄의 완전 연소를 보장해야 합니다. 석탄 입자 크기, 석탄층 두께, 공기 유입량 모두 석탄의 완전 연소에 영향을 미칩니다. 따라서 톱밥 건조기의 연료 손실을 줄이려면 이 세 가지 측면에서 시작해야 합니다. 다음은 구체적인 방법입니다.
톱밥 건조기의 연료 소비를 줄이는 세 가지 방법
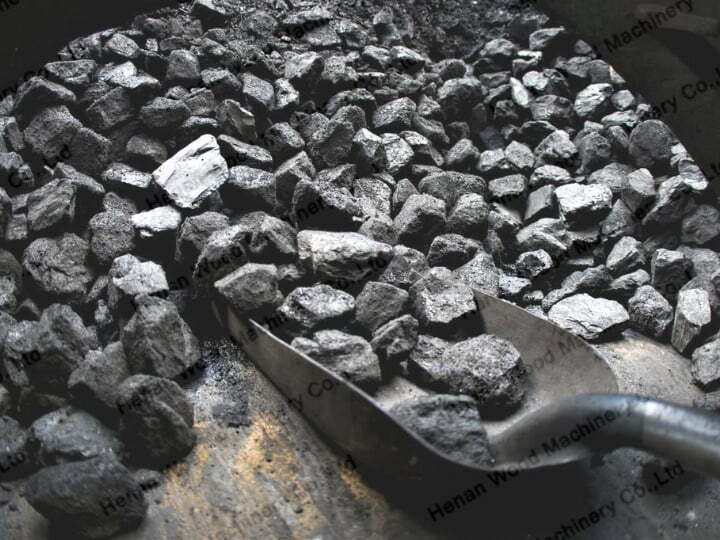
- 먼저, 석탄분말의 입자크기이다. 미분탄의 입자 크기가 미세할수록 공기와의 접촉 면적이 넓어지고 미분탄의 연소가 더 원활해집니다. 많은 실험을 통해 석탄분말의 입자크기를 0.05mm 정도로 조절하면 석탄분말이 충분히 연소되는 것을 알 수 있다.
- 다음은 석탄층의 두께입니다. 탄층의 두께도 적절한 범위 내에서 제어되어야 합니다. 석탄층 두께가 얇으면 톱밥 건조기 버너의 환기는 크지만 풍속이 균일하지 않아 석탄층에 봉황 구멍이 생겨 미분탄의 완전 연소에 도움이 되지 않습니다. 일반적으로 탄층의 두께는 150mm 정도로 조절하여 석탄분말을 충분히 연소시킨다.
- 버너에 불어넣는 공기의 양. 미분탄 연소 매체로서, 거기에 불어넣는 공기의 양도 재료의 양에 따라 결정되어야 합니다. 석탄층의 두께가 두꺼워지면 적절한 연소를 보장하기 위해 불어 넣어지는 공기의 양이 더 커집니다. 오히려 흡입되는 공기의 양이 줄어듭니다.
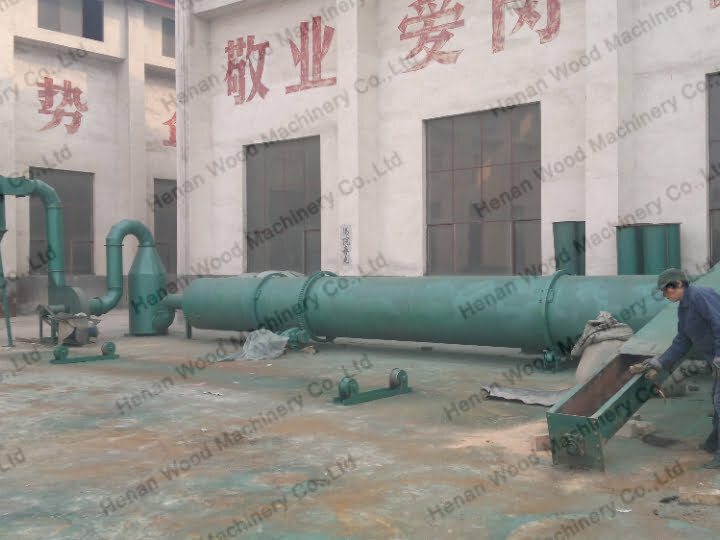